High-Temperature FeCrAl Alloy Wires: 1Cr13Al4 and 0Cr25Al5 for Reliable Heating Elements
We offer factory direct pricing and special discounts on bulk orders. Whether you need small or large quantities, our products ship quickly to ensure a reliable supply for industrial projects worldwide. Click the button below to request a quote today!
- Overview
- Specification
- Applications
- FAQs
- Recommended Products
-
1Cr13Al4: This specific alloy is known for its good balance of thermal and electrical conductivity, oxidation resistance, and mechanical strength. It can withstand temperatures up to 1200°C and is commonly used in industrial furnaces, heating elements, and other high-temperature applications.
-
0Cr25Al5: This alloy offers even higher resistance to oxidation and is capable of operating at temperatures exceeding 1300°C. Its high chromium content enhances its resistance to oxidation, making it suitable for more extreme environments, such as in furnaces that reach higher temperatures or in corrosive atmospheres.
-
Industrial Furnaces: Both 1Cr13Al4 and 0Cr25Al5 alloys are commonly used in the production of heating elements for industrial furnaces. These furnaces are used in metal processing, ceramic firing, and glass melting, where temperatures often exceed 1000°C.
-
Electric Heaters: These alloys are also used in electric heating appliances, such as water heaters, ovens, and space heaters. Their ability to maintain stability under high temperatures ensures the longevity and efficiency of these devices.
-
High-Temperature Laboratories: In laboratory environments where precise and stable heating is critical, 1Cr13Al4 and 0Cr25Al5 alloys are used for heating coils, resistance wires, and temperature sensors.
-
Power Generation: In power plants, these alloys are utilized in applications requiring efficient heat generation and resistance to oxidation, such as heating elements in steam generators and heating coils in exhaust systems.
-
Automotive Applications: High-temperature FeCrAl alloys also find use in automotive applications, particularly in exhaust systems and catalytic converters, where they help to ensure that the necessary high temperatures for chemical reactions are maintained.
-
1Cr13Al4: With a chromium content of 13% and aluminum content of 4%, this alloy provides a good balance between strength, corrosion resistance, and workability. It can withstand continuous operation at temperatures up to 1200°C, making it suitable for a wide range of applications.
-
0Cr25Al5: Featuring 25% chromium and 5% aluminum, this alloy provides superior resistance to oxidation, allowing it to operate at even higher temperatures—up to 1300°C. The high chromium content also gives it excellent durability in corrosive environments, ensuring a long service life in demanding applications.
-
High-Temperature Stability: The ability to withstand prolonged exposure to high temperatures without degradation is essential for industrial applications. Both 1Cr13Al4 and 0Cr25Al5 provide excellent stability even in extreme environments.
-
Oxidation Resistance: The alloys' resistance to oxidation ensures they will not deteriorate over time, even in high-oxygen environments, which is a common challenge in many industrial processes.
-
Durability and Longevity: FeCrAl alloy wires are expected to provide long service life, reducing the need for frequent replacements and minimizing downtime. This helps businesses reduce operational costs and improve overall productivity.
-
Efficient Heat Transfer: The alloys also ensure efficient heat generation and transfer, which is crucial for energy savings and achieving the desired temperatures in various industrial processes.
-
Cost-Effectiveness: While FeCrAl alloys may be more expensive than some other materials, their durability and longevity make them a cost-effective solution in the long run, as they require less maintenance and replacement.
FeCrAl (Iron-Chromium-Aluminum) alloys, including 1Cr13Al4 and 0Cr25Al5, have become the go-to materials for manufacturing high-temperature heating elements in various industrial applications. These alloys offer a combination of durability, excellent oxidation resistance, and high-temperature stability, making them ideal for applications requiring reliable and long-lasting performance. This article explores the features of FeCrAl alloys, particularly 1Cr13Al4 and 0Cr25Al5, their applications, manufacturing processes, and how they meet user demands in high-temperature environments.
Material Introduction
FeCrAl alloys are a family of materials composed primarily of iron, chromium, and aluminum. The addition of chromium and aluminum provides these alloys with exceptional resistance to oxidation and corrosion, especially at elevated temperatures. This makes FeCrAl alloys an excellent choice for use in heating elements that are subjected to harsh conditions.
Applications
FeCrAl alloys, particularly 1Cr13Al4 and 0Cr25Al5, are widely used across various industries that require heating elements capable of enduring high temperatures and harsh conditions. Some of the most common applications include:
Alloy Grades and Specifications
FeCrAl alloys come in different grades, with 1Cr13Al4 and 0Cr25Al5 being two of the most commonly used grades for heating elements:
Manufacturing Process
The production of FeCrAl alloy wires begins with the careful selection of raw materials. The alloy is made by combining iron, chromium, and aluminum in precise proportions, typically through a melting process in an induction furnace. The molten metal is then cast into billets or ingots and processed through various stages, such as extrusion, drawing, and annealing, to form the final wire product.
The wire undergoes stringent quality control measures during production to ensure that it meets the required specifications for temperature resistance, electrical conductivity, and mechanical strength. Heat treatments, such as annealing, may be applied to optimize the material’s performance in specific applications. The result is a highly durable, heat-resistant wire that maintains stable electrical and thermal properties even at elevated temperatures.
Meeting User Demands
FeCrAl alloys like 1Cr13Al4 and 0Cr25Al5 are designed to meet the rigorous demands of industries that require reliable, long-lasting heating elements. Users typically prioritize the following qualities when selecting heating element materials:
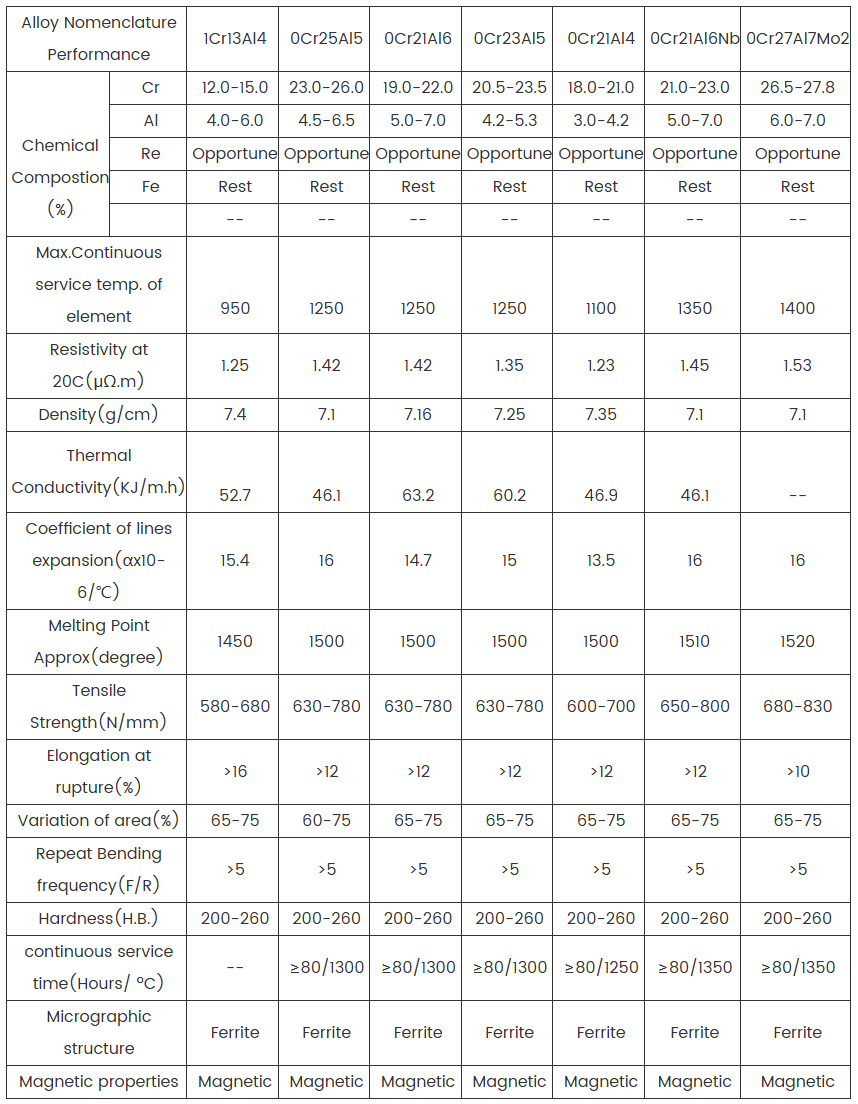
FAQs:
How long is the delivery time?
It depends on the quantity of the order, 10-30 days for small orders. For large orders, it takes 60 days.
Do you accept OEM/ODM production?
Yes! We accept OEM/ODM production. You can send us your samples or drawings.
How do you control the quality of your products? Do the chemical properties of the products meet the quality standards?
With professional quality team, advanced product quality planning, strict implementation and continuous improvement, we will issue product quality inspection certificate, including chemical analysis report.
Can your company provide detailed technical data and drawings?
Yes, you can. Please tell us the products and applications you need, and we will send you detailed technical data and drawings for your evaluation and confirmation.
How do you handle pre-sale and after-sale service?
We have a professional business team who will work one-on-one to protect your product needs, and if you have any questions, he can answer them for you!
Can I visit your factory before placing an order?
Yes, you are welcome to visit our factory. We are glad to have the opportunity to get to know each other.
Where is your production base?
We manufacture our products in Jiangsu, China and ship them from China to your country as soon as possible, which usually depends on your product requirements and quantity.
Can you send samples?
Yes, we can.