CuNi2 Alloy Wire – Perfect for Seawater Cooling Systems and Chemical Processing Equipment
We offer factory direct pricing and special discounts on bulk orders. Whether you need small or large quantities, our products ship quickly to ensure a reliable supply for industrial projects worldwide. Click the button below to request a quote today!
- Overview
- Specification
- Applications
- FAQs
- Recommended Products
Material Introduction
CuNi2 alloy wire is a copper-nickel alloy composed of 98% copper and 2% nickel. This alloy is known for its excellent resistance to corrosion, particularly in marine environments, and its outstanding mechanical properties. The addition of nickel enhances the material's strength, stability, and resistance to various corrosive agents, making it an ideal choice for demanding applications in seawater cooling systems and chemical processing equipment. CuNi2 alloy wire also maintains good electrical conductivity and thermal properties, making it suitable for a variety of industrial and marine applications.
Key characteristics of CuNi2 alloy wire include excellent corrosion resistance, mechanical strength, and a balance between electrical and thermal conductivity. This wire also possesses ductility and malleability, allowing it to be used in various applications where flexibility is required.
Applications
CuNi2 alloy wire is particularly suitable for environments where both corrosion resistance and mechanical performance are critical. Below are some of its key applications:
Seawater Cooling Systems
CuNi2 alloy wire is commonly used in seawater cooling systems in marine environments. It is used in heat exchangers, cooling coils, and condensers, where it offers protection against the corrosive effects of seawater. The alloy’s excellent resistance to corrosion ensures that the cooling systems remain functional and efficient, even in harsh marine conditions.
Chemical Processing Equipment
In chemical processing industries, CuNi2 alloy wire is used in various applications where resistance to corrosive substances is essential. It is commonly used for piping systems, valves, and fittings in chemical processing plants. Its ability to resist a wide range of chemicals ensures the safe and efficient transport of corrosive fluids. Additionally, CuNi2 alloy wire is employed in chemical reactors and other equipment exposed to aggressive chemicals, ensuring reliable performance in critical processes. The alloy is also used in electrochemical applications, such as electrodes and anodes, where its resistance to oxidation and corrosion is a key factor in stable operation.
Marine Applications
Given its corrosion resistance to seawater, CuNi2 alloy wire is commonly used in various marine applications, including shipbuilding, offshore oil and gas platforms, and submarines. It is used for components exposed to the harsh marine environment, ensuring the longevity and reliability of marine infrastructure. Its durability makes it a valuable material in ensuring the operational integrity of submerged systems.
Grades and Characteristics
CuNi2 alloy wire is characterized by its composition of 98% copper and 2% nickel. The addition of nickel enhances the alloy's corrosion resistance, mechanical strength, and resistance to various chemicals, making it suitable for use in marine and chemical processing systems. CuNi2 alloy wire is also stronger and more durable than pure copper, making it ideal for applications where the wire is subjected to mechanical stress or high-pressure environments.
The wire provides a cost-effective solution for industrial applications, offering good performance at a lower cost compared to higher-nickel alloys. This makes it an attractive option for large-scale manufacturing and applications that require durability and resistance to corrosion without the high expense associated with other alloys.
Manufacturing Process
The manufacturing process of CuNi2 alloy wire involves several key steps:
Alloy Preparation and Melting
Copper and nickel are melted together to form the alloy, with precise control over the ratio to ensure uniform composition. The process is critical to maintaining the alloy's resistance to corrosion and mechanical strength.
Wire Drawing
After the alloy is formed, it undergoes wire drawing, where the metal is passed through progressively smaller dies to achieve the desired wire diameter. The wire drawing process helps enhance the mechanical properties of the alloy and ensures uniformity across the wire.
Annealing
To relieve stress and increase ductility, the wire is annealed at specific temperatures. This step ensures the wire can be easily shaped and manipulated for use in various applications, while maintaining its corrosion resistance and strength.
Surface Treatment
CuNi2 alloy wire may undergo surface treatments, such as passivation or coating, to further enhance its resistance to corrosion and oxidation, especially in highly corrosive environments like seawater and chemical processing plants.
Quality Control and Testing
Throughout the manufacturing process, strict quality control is applied. The wire undergoes various tests to ensure it meets the required standards for mechanical strength, conductivity, and corrosion resistance. This ensures that CuNi2 alloy wire performs reliably in demanding applications.
User Requirements
When selecting CuNi2 alloy wire, users typically have the following requirements:
Corrosion Resistance
Given that CuNi2 is primarily used in marine and chemical environments, users require the alloy wire to offer exceptional resistance to seawater and chemicals. This resistance is essential to ensure long-lasting, trouble-free operation in harsh conditions.
Mechanical Strength
CuNi2 alloy wire must possess adequate mechanical strength to endure the pressures and mechanical stresses often encountered in industrial and marine applications. This includes the ability to resist deformation and failure under high-stress conditions.
Thermal and Electrical Performance
Users may require the wire to maintain stable thermal and electrical conductivity, especially in cooling systems or heating elements. CuNi2 alloy wire offers balanced thermal and electrical properties, ensuring efficient heat transfer and energy use.
Durability
CuNi2 alloy wire must be durable and resistant to wear and tear over extended periods of exposure to corrosive elements. Users need a product that can withstand harsh operating conditions and maintain its integrity for long-term use.
Cost-Effectiveness
While CuNi2 alloy wire offers excellent performance, users also look for cost-effectiveness in their materials, particularly for large-scale applications. CuNi2 provides a good balance between performance and cost, making it a popular choice for industrial and marine applications.
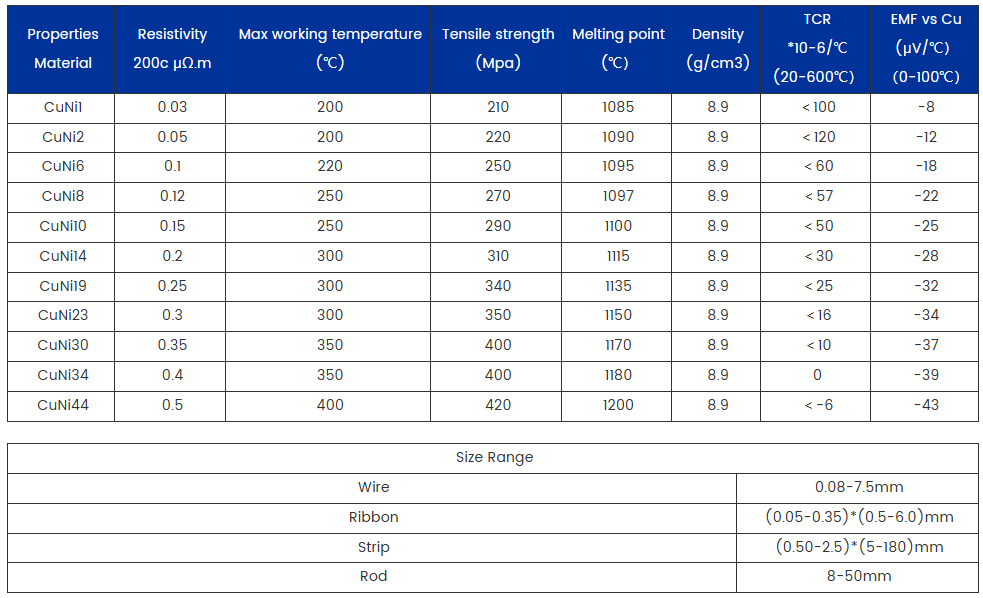
FAQs:
How long is the delivery time?
It depends on the quantity of the order, 10-30 days for small orders. For large orders, it takes 60 days.
Do you accept OEM/ODM production?
Yes! We accept OEM/ODM production. You can send us your samples or drawings.
How do you control the quality of your products? Do the chemical properties of the products meet the quality standards?
With professional quality team, advanced product quality planning, strict implementation and continuous improvement, we will issue product quality inspection certificate, including chemical analysis report.
Can your company provide detailed technical data and drawings?
Yes, you can. Please tell us the products and applications you need, and we will send you detailed technical data and drawings for your evaluation and confirmation.
How do you handle pre-sale and after-sale service?
We have a professional business team who will work one-on-one to protect your product needs, and if you have any questions, he can answer them for you!
Can I visit your factory before placing an order?
Yes, you are welcome to visit our factory. We are glad to have the opportunity to get to know each other.
Where is your production base?
We manufacture our products in Jiangsu, China and ship them from China to your country as soon as possible, which usually depends on your product requirements and quantity.
Can you send samples?
Yes, we can.